The Best Strategy To Use For Indonesia Furniture Manufacturers
The Best Strategy To Use For Indonesia Furniture Manufacturers
Blog Article
All about Indonesia Furniture Manufacturers
Table of ContentsNot known Factual Statements About Indonesia Furniture Manufacturers A Biased View of Indonesia Furniture ManufacturersThe Definitive Guide for Indonesia Furniture ManufacturersSome Known Questions About Indonesia Furniture Manufacturers.The smart Trick of Indonesia Furniture Manufacturers That Nobody is Talking About
However, there are some drawbacks to acquiring from a furnishings producer. For one, you may need to wait longer to obtain your furniture given that it's being tailored. In addition, you might not be able to see or touch the item before you purchase it. A furnishings seller is a business that markets furnishings made by numerous suppliers.When you purchase from a furnishings store, you're buying a piece of furniture that's already been made and prepares to be shipped to your home. One of the advantages of purchasing from a furniture seller is that you can usually see and touch the item prior to you buy it.
At BH Furniture, our team believe in setting brand-new standards for quality in the manufacturing of industrial furnishings - Indonesia furniture manufacturers. Our commitment to advancement has led us to embrace cutting-edge automation technology, changing the method we produce furniture and moving us to the forefront of the market. Gone are the days of manual work dominating the production flooring
Our equipment functions perfectly, directed by the specific parameters established by our skilled engineers, making sure regularly high-grade outcome. State farewell to production delays and overtime expenses. Our automated systems operate relentlessly, 24/7, assuring a steady and undisturbed operations. This means we not just meet however surpass delivery due dates, offering our customers with a degree of reliability that typical production approaches merely can't match.
Things about Indonesia Furniture Manufacturers
Our manufacturing ability has actually risen, permitting us to fulfill the needs of also the biggest tasks without endangering on high quality. As your partner in commercial furniture services, we can effortlessly scale our result to suit your demands, despite the range. While typical manufacturing counts greatly on manual work, our automated systems have actually significantly reduced our dependancy on a huge labor force.
Furnishings manufacturing is a complex process that involves numerous phases, from creating and material selection to production and setting up. At each phase, there is a possibility of problems or mistakes that can endanger the high quality of the final item. To make certain that furnishings is of premium quality, furniture makers execute quality assurance procedures to recognize and rectify any concerns that might occur throughout production.
The evaluation process must cover various elements, such as assembly, coating, colour, design, product packaging, labelling, and marking. By implementing a strenuous assessment procedure, makers can ensure their items meet the necessary top quality, security, and toughness requirements. They also give the versatility to resolve problems and make corrections prior you can try these out to finishing the final product.
The procedure starts with the basic materials assessment to the last setting up of the furniture. The objective is to guarantee that the items are devoid of issues, safe, and fulfill the customer's expectations. Furnishings quality requirements are collections of guidelines and requirements for furniture production. They specify the required top quality degree of furniture manufacturing and cover elements such as safety, resilience, toughness, and environmental influence.
The Indonesia Furniture Manufacturers Ideas

To guarantee their furniture items can withstand numerous climate components, consisting of sun, rainfall, snow, and wind, manufacturers must think about internationally identified criteria that make up evaluations and screening. Below are a few of the requirements to maintain in mind: ASTM F1561-03 is a global conventional established by the American Area of the International Association for Screening Materials (ASTM).
UL 962 is a worldwide safety and security standard established by Underwriters Laboratories (UL), an independent international supply safety options business. The conventional applies to family and business home furnishings, including outside furnishings.
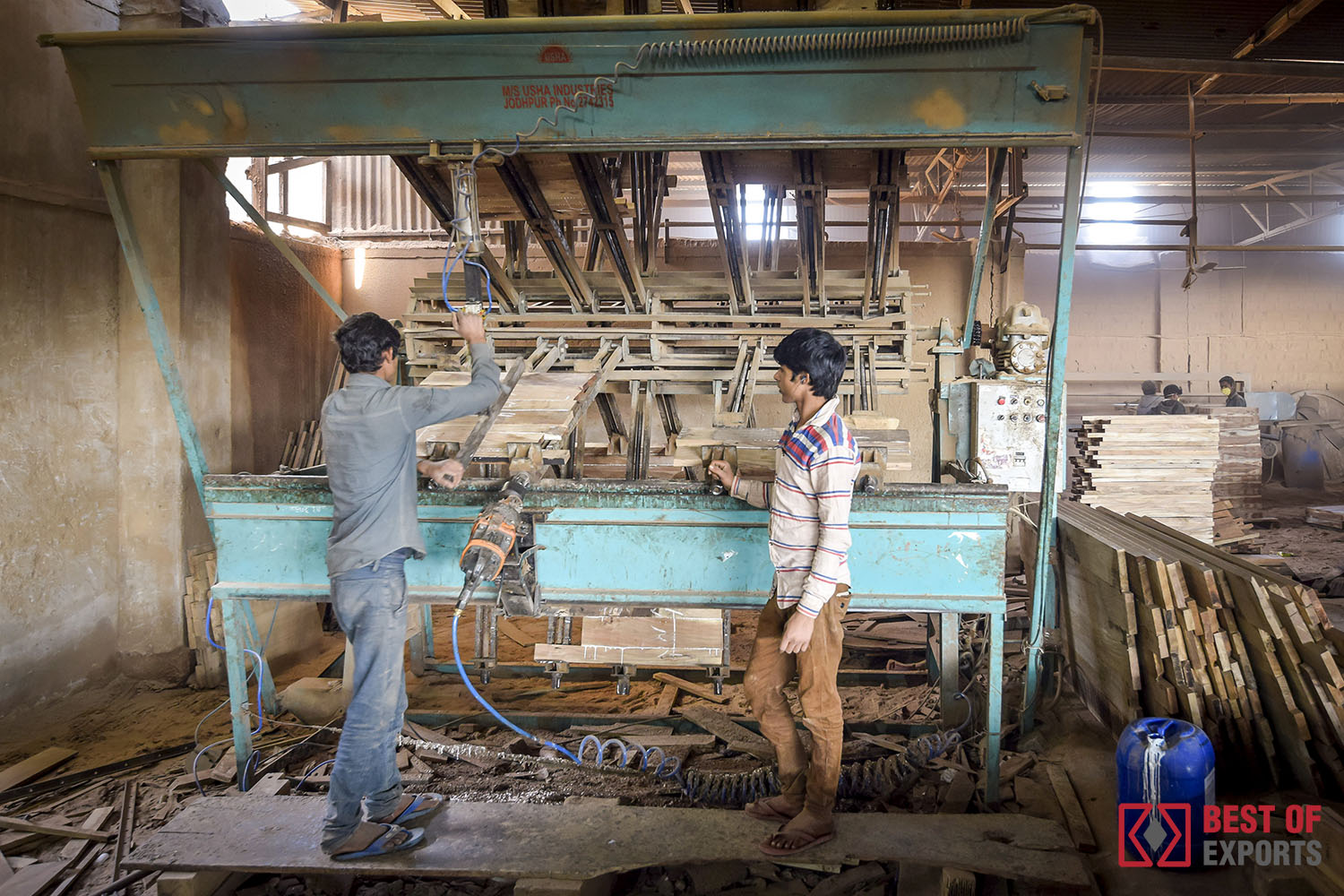
Getting The Indonesia Furniture Manufacturers To Work
It aids to determine defects in the furnishings and review its performance and conformity with the called for quality criteria. These examples generally stand for the various kinds of furnishings that they generate.
This might entail a mix of various examinations, consisting of toughness screening, durability testing, security screening, and ecological effect testing. The samples are then checked for various high quality specifications, such as stamina, toughness, safety, and ecological influence. The outcomes see page are after that reviewed to identify whether the products meet the required quality standards.

Generally, every retail store furnishings is various. Layouts conference customer comfort Optimizing area use in storage space, display, step, visitor seats and walkways Guaranteeing simplicity of accessibility to items for tests and acquisition Creating modular furniture that is very easy to relocate and refit Meeting safety requirements of consumers A fast TAT from layout to manufacturing and installation with very little mistakes can assist resolve the above concerns.
Our Indonesia Furniture Manufacturers PDFs
A developer can comprehend the market fads and be prepared with ingenious designs in advance of time. Read below: Exactly How DriveWorks Assists You to Reduce Lead Time in Production Developers usually need to change the sizes and shapes of furnishings at a moment's notification. These may have various aesthetic and functional demands like front workdesk, and servicing workdesk that vary in dimensions.
Improves product quality and decreases scrap. Field guideline records along with amount launches are also generated for retail shop furnishings installments. Style iterations and conflicts are reduced, and the store floor can begin producing on the day of sales.
It is a very competitive market, with organizations aiming to maintain up with altering consumer needs and the latest technical trends. Today's consumers are more likely to prefer furnishings that is tailored and made with sustainable materials.
Report this page